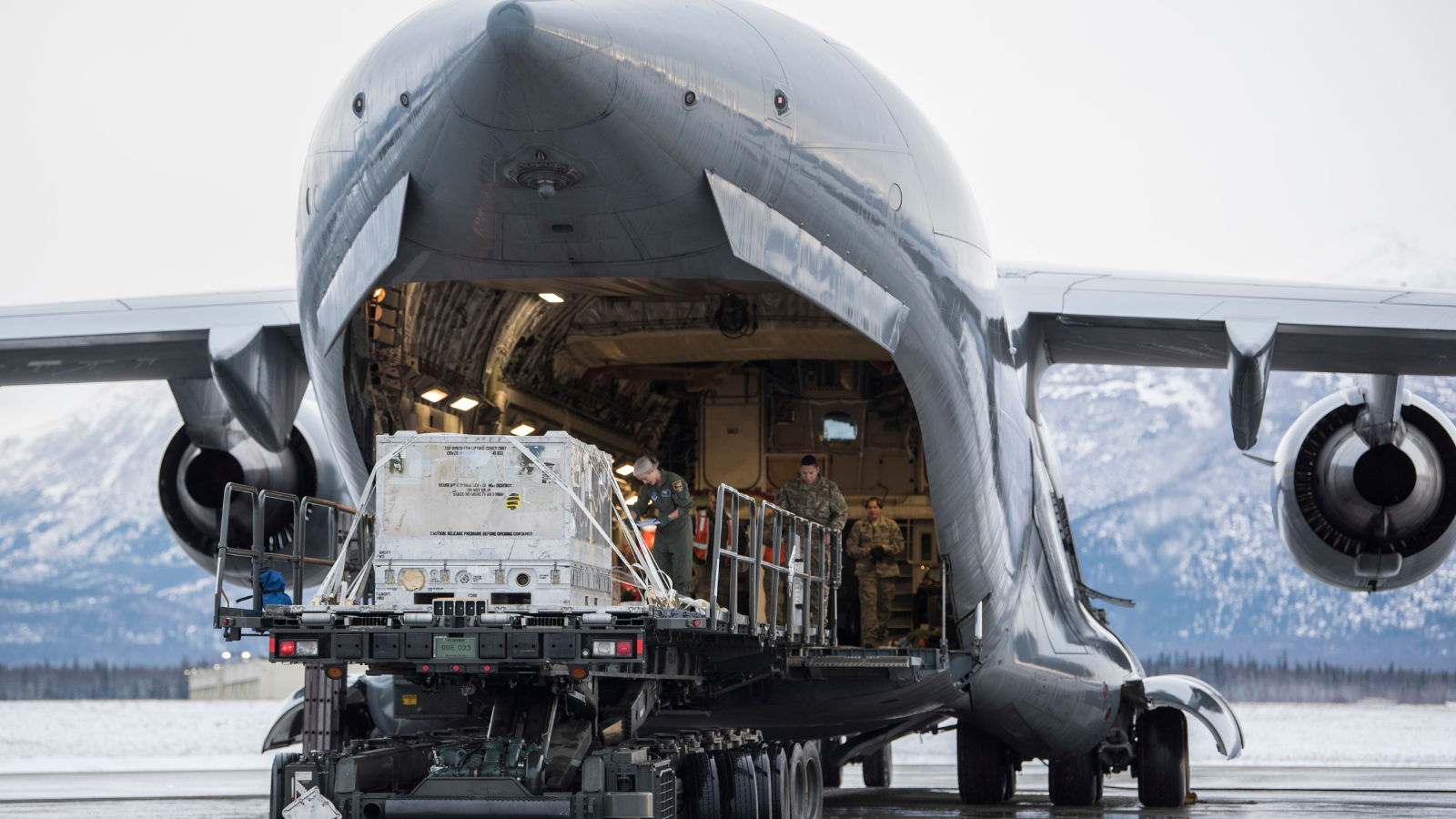
Innovating Logistics: The Birth of the Rapid Yeti Program
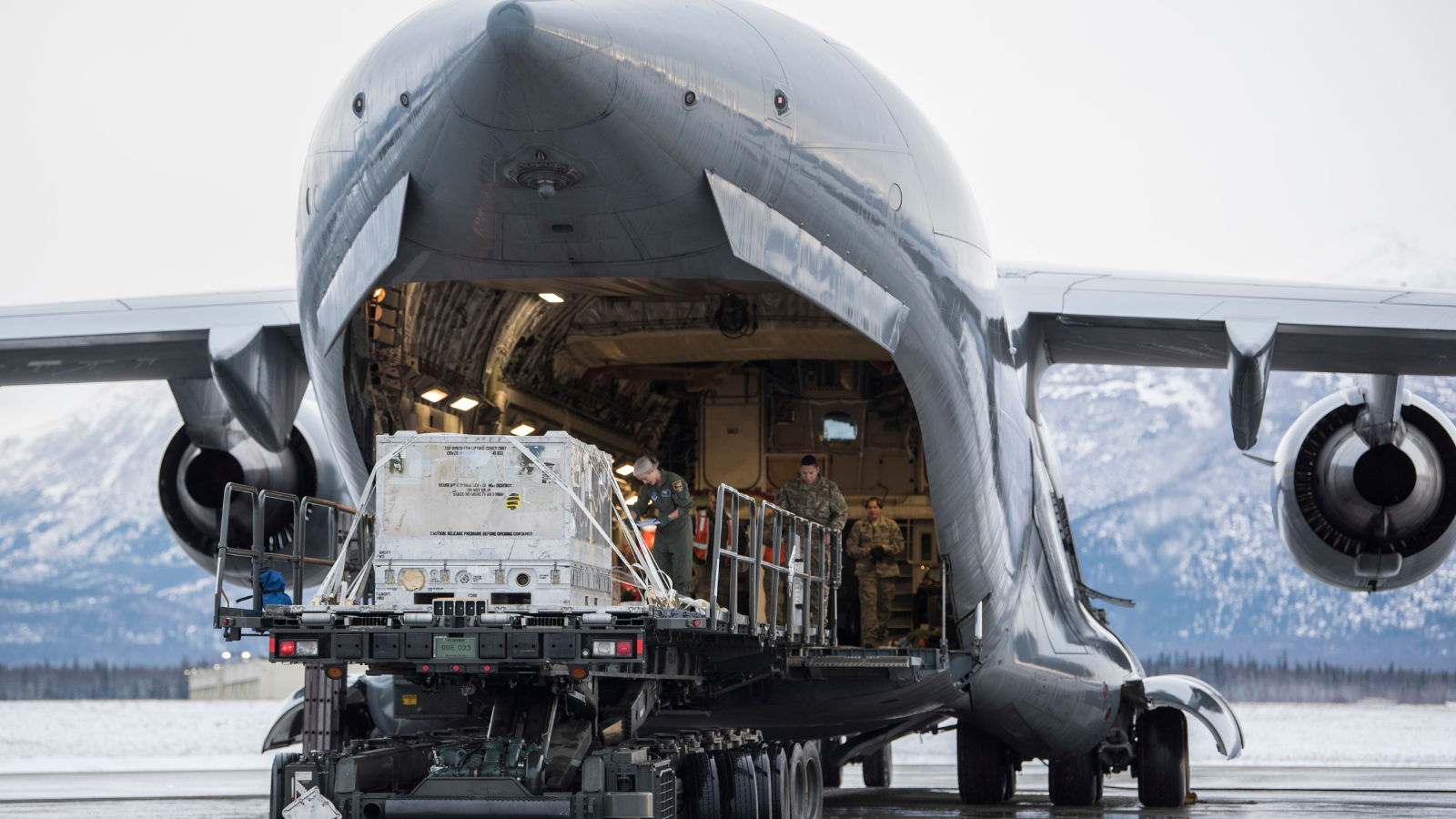
More than 4,000 miles separate Elmendorf Air Force Base in Anchorage, Alaska and Texas A&M University in College Station, Texas. However, the National Security Innovation Network (NSIN) connected them for an innovative logistics project that could transform cargo unloading in austere environments.
Known as Rapid Yeti, the project grew from the brainchild of a singular service member working in logistics to a multi-organizational collaboration bridging multiple military stakeholders and academia to build a 3D prototype ready for testing and further development.
The initial idea came from a front-line service member working in logistics. He took the idea to his leadership who directed him to Arctic Spark, which reviews innovation initiatives and determines their merit and viability. Arctic Spark reached out to NSIN to help take the project from idea to reality.
“This was a great project to put it out into the world of innovation and we got connected with NSIN, which explained the capstone program,” said Master Sgt. Brian Crea, Director of Innovation at Arctic Spark. “They [NSIN] would outsource the idea to colleges and see who wants to take a crack at solving it. Texas A&M picked it up and their engineering students really did phenomenal work in making an idea on paper into something real.”
Replacing an Outdated Method
Currently, the Air Force uses a crude yet effective method developed during the Vietnam War to unload heavy cargo from aircraft in austere environments.
Known as Combat Offload Method B, this method utilizes steel drum barrels placed outside the rear cargo door to slide weighty objects out of the plane to the tarmac. While the process works, it is cumbersome and risky.
The method lines up eight barrels – four on each side – parallel to the back ramp of the C-130. The pallets securing the engine stand are chained to the tailgate of a truck which will help pull the equipment off the C-130 as it slowly taxis forward. As the equipment is carefully removed, an airman from each side slides a barrel underneath the corners of the pallet, creating a solid foundation for it to rest up. The process continues until all barrels are all placed and the equipment is completely removed from the aircraft.
The primitive tools, and communication requirements between the unloading team and the pilot contribute to a complicated process orchestrated under challenging environments.
Staff Sgt. Regina Edwards, 19th Airlift Wing Public Affairs, explained that this process must be synchronized, which demands constant communication from the loadmasters, air transportation specialists, and aircrew. While this method is performed, the aircraft’s engine remains running so the pilots can slowly taxi and release the equipment.
Rapid Yeti was designed to remove the need to taxi the plane and eliminate the need for barrels. By doing so, logistics teams could unload cargo faster and more safely, an important need while working in areas that lack traditional unloading infrastructure.
From Idea to Prototype
The Air Force wanted an external partner to help with the engineering and building of Rapid Yeti. While the Air Force had the concept of what it wanted, it needed support to make that concept a reality.
Over two semesters, the Texas A&M students worked closely with the Air Force, holding weekly meetings to refine the design. The result was a 3D-printed model of the Rapid Yeti cart, ready for further testing and development. Part of that design also includes different sizes of the Rapid Yeti known as Hulk and Wolverine that are also under consideration for further development.
As of now, Rapid Yeti remains a detailed design awaiting funding for prototype production and testing. The project aims to create two prototypes for initial trials, with plans to refine the design based on feedback and operational testing. The ultimate goal is to implement Rapid Yeti across the Air Force, enhancing cargo handling capabilities in challenging environments.
“Rapid Yeti shows how an idea can evolve into action,” said Tanya Parypa, NSIN Northwest Regional Director. “A service member identified a problem and created a potential solution that could make his job easier. Arctic Spark encouraged that development and leveraged NSIN to find the best partners to take that idea to the next level.”
Recent discussions with senior Air Force officials and presentations to the Air Force Chief Scientist have highlighted the program’s potential. Additionally, the project has garnered interest from various wings within the Pacific Air Forces (PACAF), with efforts underway to secure momentum funds for broader testing and deployment.
“Now you have a system where you can use multiple Yetis, sliding them on and off without putting barrels under the ramp,” Crea said. “The jet stays still, unlike the other method where it had to taxi forward. It’s way more safe and way more robust.”
Photo: U.S. Air Force Airmen with the 732nd Aircraft Mobility Squadron unload cargo onto a C-17 Globemaster III at Joint Base Elmendorf-Richardson, Alaska, Dec. 1, 2018. JBER mission operations continue following a 7.0 earthquake hit to Anchorage, Alaska, on Nov. 30. Photo by Airman 1st Class Caitlin Russell.
About National Security Innovation Network
NSIN is a program office in the U.S. Department of Defense (DoD), nested within the Defense Innovation Unit (DIU). We are set up to collaborate with a wide variety of innovators to include universities, researchers, students, entrepreneurs and start-ups. We create opportunities for collaboration across communities and connect those that might not traditionally work in national security. Together, we help drive national security innovation and develop technologies that directly support the individuals responsible for protecting our country.
For more information or interview requests with Team NSIN, please contact us at media@nsin.mil.